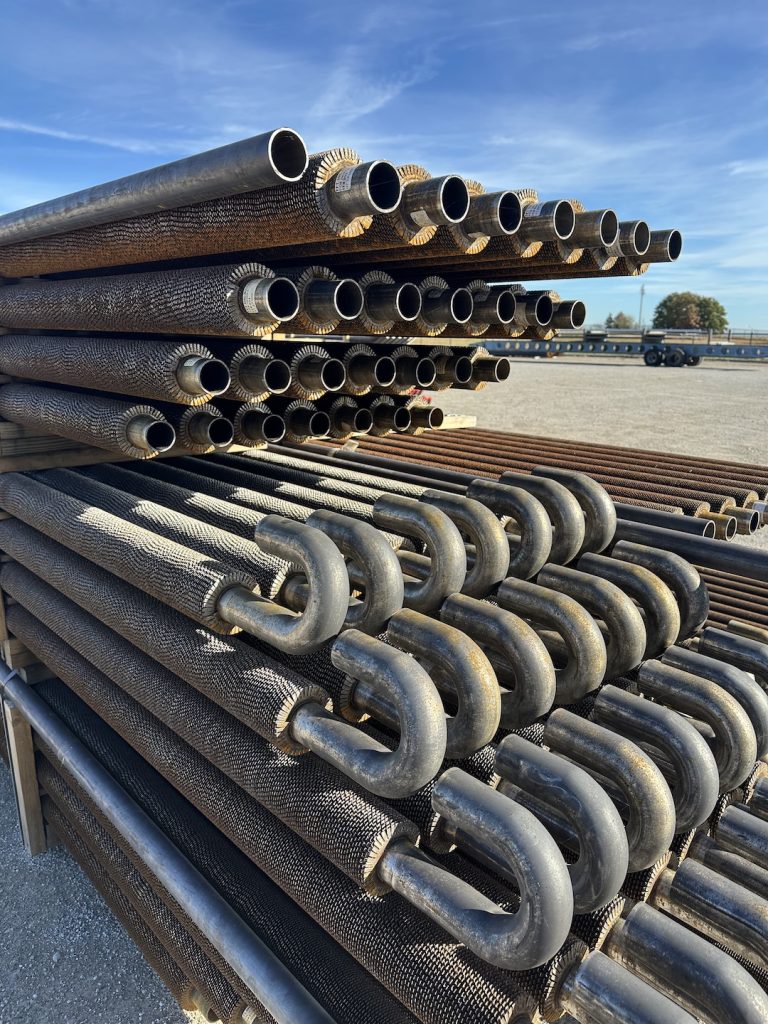
How Tulsa Fin Tube Creates Super-Strong Finned Tubes
If you’ve ever wondered how finned tubes are made (or even what they are), you’re in the right place! At Tulsa Fin Tube, we use a special welding process to attach metal fins to tubes, making them super efficient at transferring heat.
Sound complicated? Don’t worry—we’ll break it down so it’s easy to understand!
What Are Finned Tubes, and Why Do They Need to Be Welded?
Imagine a regular metal tube—it moves heat from one place to another, but it’s not very efficient on its own. Now, imagine that same tube wrapped in metal fins that increase the surface area, allowing heat to transfer much faster. That’s exactly what a finned tube does!
But here’s the catch—those fins need to be strongly attached to the tube to work properly. If they’re loose or weak, they won’t transfer heat efficiently, and the whole system could fail.
That’s where high-frequency resistance welding (HFRW) comes in!
How Tulsa Fin Tube’s Welding Process Works
Think of HFRW as a high-tech way to glue metal together—but without the glue! Instead of using extra materials, we use heat and pressure to fuse the fin to the tube, creating an incredibly strong bond.
Here’s how it works, step by step:
- A metal strip (the fin) is wrapped around the tube in a spiral shape. This gives the tube more surface area to transfer heat.
- We apply high-frequency electrical current to heat up just the right spot. Instead of heating the whole tube, we focus the heat exactly where the fin and tube touch.
- The heat softens the metal, and pressure pushes the fin and tube together. This creates a permanent bond—no filler materials, just pure metal-on-metal fusion.
- Cooling water prevents overheating and keeps the weld clean. This helps maintain quality and ensures a strong, even bond.
The result? A perfectly welded, long-lasting finned tube that can handle extreme temperatures and pressures without breaking down.
Why Tulsa Fin Tube’s Welding Process is the Best
1. More Precision, Less Waste
Instead of heating the whole tube, we focus the energy exactly where it’s needed, making the process more efficient and reducing waste.
2. Smart Use of Electricity
Our process takes advantage of two key electrical effects:
- Skin Effect: The electric current stays on the outer surface of the tube, so it doesn’t overheat the inside.
- Proximity Effect: The current naturally flows to the point where the fin meets the tube, ensuring a strong bond.
3. Cleaner Welds with Less Mess
When metal gets welded, tiny bits of material—called spume—can fly off. We control this with cooling water, keeping the weld area clean and preventing defects.
4. The Right Amount of Power for Every Weld
Too much power = a weak, messy weld.
Too little power = the fin won’t stick properly.
We monitor every weld in real-time to make sure it’s just right—strong, smooth, and built to last.
Why Should You Care?
- Better welding means better finned tubes, and better finned tubes mean:
- Longer-lasting equipment
- More energy efficiency
- Lower costs and fewer breakdowns
At Tulsa Fin Tube, we’ve perfected this process to make sure our customers get the best quality, every time.
Need High-Quality Finned Tubes? Let’s Talk!
If you need finned tubes that perform under pressure, Tulsa Fin Tube has the experience and technology to get the job done right. Contact us today for a custom quote and let’s build something great together!