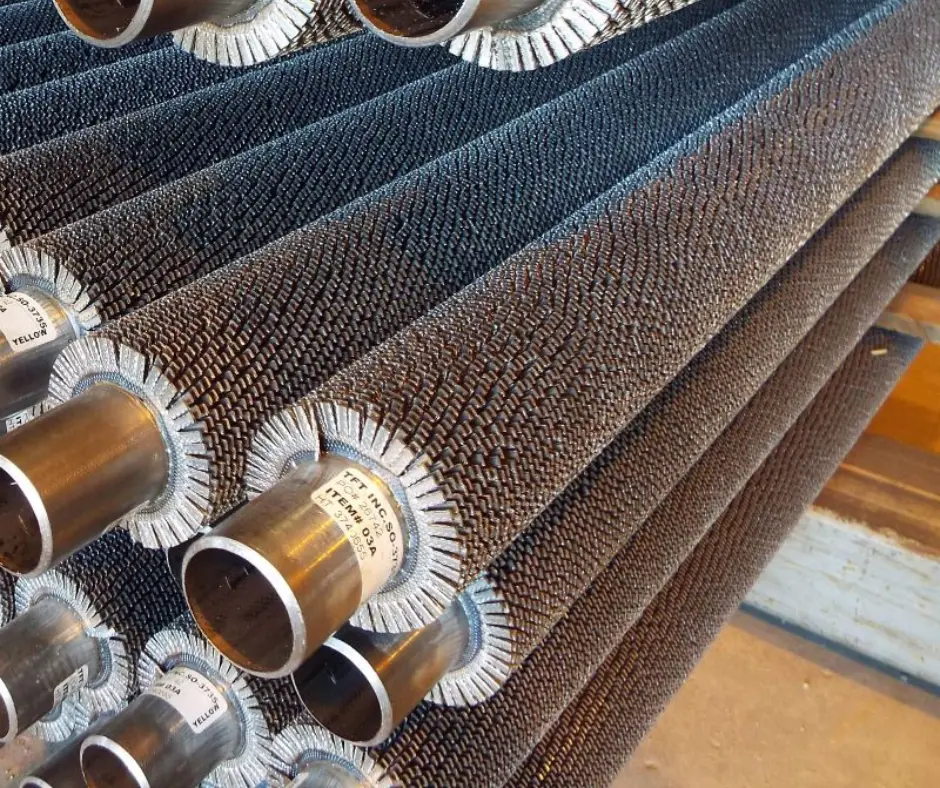
How Can Custom Cooling Solutions Improve the Manufacturing Process?
Discover how integrating custom cooling solutions can revolutionize your manufacturing efficiency and product quality.
Overview of Custom Cooling Solutions
This refers to specially designed and engineered systems tailored to meet the unique cooling requirements of different manufacturing processes.
Unlike off-the-shelf cooling products, these solutions are developed with a specific industrial application in mind, ensuring they precisely address the heat management challenges faced by manufacturers.
Implementing these systems allows for more efficient heat dissipation, resulting in improved machinery lifespan, enhanced product quality, and a more sustainable manufacturing environment.
These systems range from liquid cooling setups specifically designed for heavy machinery to air-cooled systems for electronics manufacturing, all constructed to optimize performance and energy consumption.
Benefits
One significant advantage of custom cooling solutions is their ability to significantly reduce operational costs. By optimizing cooling processes, manufacturers can see a decrease in energy consumption, leading to lower utility bills.
Enhanced cooling efficiency also means less wear and tear on machinery, reducing maintenance costs and downtime.
Moreover, by maintaining optimal temperatures, these solutions help in preserving the structural integrity and quality of produced goods, minimizing waste and ensuring consistent product quality.
This thermal management directly contributes to higher satisfaction rates among customers and strengthens brand reliability.
Finally, customized cooling solutions support sustainability goals. Advanced technologies enable more precise cooling, which, besides cutting costs, reduces the carbon footprint of manufacturing processes.
This is crucial for businesses aiming to comply with increasing environmental regulations and seeking to position themselves as eco-conscious brands in a competitive market.
Different Manufacturing Processes
The applicability of custom cooling solutions spans across a wide array of manufacturing sectors.
For instance, in the food and beverage industry, these systems are crucial for maintaining the freshness of products through refrigeration technologies that prevent spoilage during production and storage.
In the electronics sector, custom cooling is essential for preventing overheating in densely packed components, which could otherwise lead to equipment failure and data loss.
Similarly, in the automotive industry, custom solutions manage the immense heat generated during manufacturing processes, protecting sensitive electronics and ensuring the safety and efficacy of vehicle production.
Implementation
The implementation of custom cooling solutions begins with a detailed analysis of the manufacturing process to identify specific heat management challenges.
This involves consulting with cooling solution specialists who can design a system that not only meets the immediate cooling needs but also scales with future production enhancements.
Choosing the right partner for implementing these solutions is critical.
It requires selecting a vendor with a proven track record in your industry, who can offer innovative solutions and comprehensive support, from design to installation and beyond.
Measuring the Impact on Manufacturing Efficiency
To truly gauge the effectiveness of custom cooling solutions in improving manufacturing processes, businesses must adopt a metric-based approach.
Key performance indicators (KPIs) such as energy consumption, product waste reduction, and equipment downtime can offer insight into the impact of these cooling systems.
Further, regular audits of the cooling system’s performance ensure that it continues to meet the evolving demands of the manufacturing process.
Uptime enhancements and energy efficiency gains are tangible evidence of the benefits that it brings to the table. Contact us to today to learn more!
It’s more than just an upgrade; it’s a transformative approach to enhancing your manufacturing process. Read about the Latest Advances in Fin Tube Technology next!