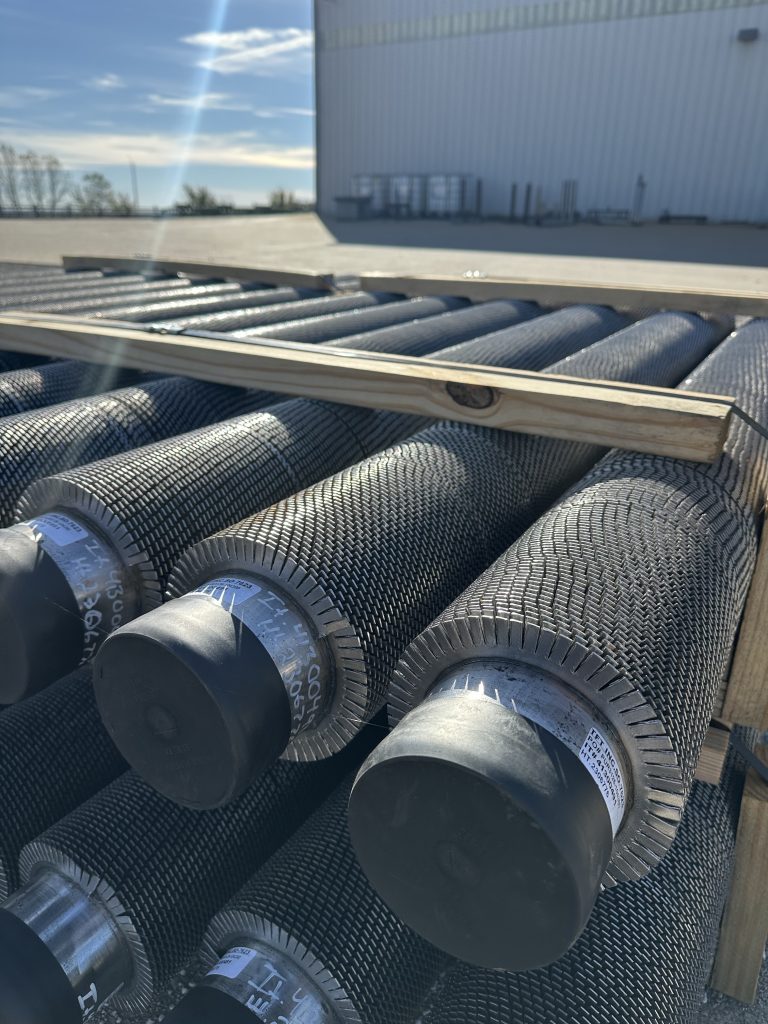
Heat Exchanger Design: Efficiency in Industrial Applications
Welcome to the latest post in our engineering insights series! Today, we delve into the fascinating world of heat exchangers. Heat exchangers are vital components that serve critical roles across various industries, including chemical plants, refineries, HVAC systems, and power generation.
Moreover, these designs facilitate essential energy transfer processes, contributing significantly to heating, cooling, and maintaining thermal stability in industrial systems. Because their efficiency directly impacts operational costs and environmental outcomes, heat exchangers are indispensable in modern industrial applications. In this blog, we explore recent innovations in heat exchanger design that set new standards for efficiency and industrial effectiveness.
The Role of Heat Exchangers in Industry
Heat exchangers transfer heat between fluids, gases, or solids without mixing, ensuring thermal energy management across many industrial applications. For example, they regulate reaction temperatures in chemical processing and are essential for steam generation and cooling in power plants. Furthermore, HVAC systems rely on heat exchangers to control air and water temperatures, ensuring comfort in residential and commercial spaces. Efficient heat exchangers reduce energy consumption, operational costs, and emissions, aligning with global sustainability and energy efficiency goals.
Breakthroughs in Heat Exchanger Design
-
Additive Manufacturing (3D Printing)
Additive manufacturing, or 3D printing, revolutionizes heat exchanger design by enabling intricate structures previously impossible with traditional methods. For instance, engineers use 3D printing to implement optimized geometries, enhancing heat transfer efficiency while minimizing material waste and costs.
Additionally, these designs include lattice structures and cooling channels, increasing surface area and turbulence, improving heat transfer coefficients effectively. Customizable designs reduce additional fittings and create compact, lightweight exchangers that simplify installation and maintenance processes. Advanced materials like composites and high-performance alloys offer superior thermal properties and corrosion resistance in challenging environments.
-
Graphene-Enhanced Materials
Graphene’s exceptional thermal conductivity transforms heat exchanger materials, boosting efficiency while enhancing durability and resistance to corrosion. For instance, graphene composites facilitate faster heat dispersion, optimizing thermal management systems for industries requiring precision and high performance. Furthermore, these materials reduce maintenance needs, improve reliability, and extend the lifespan of heat exchangers under harsh conditions.
-
Digital Twin Technology
Digital twin technology creates virtual replicas of devices, allowing engineers to simulate performance and optimize heat exchanger designs effectively. This innovation supports predictive maintenance, minimizing downtimes and enhancing the longevity of exchangers in industrial applications. By leveraging real-time data, engineers refine designs and ensure peak performance under various environmental conditions proactively.
-
Enhanced Surface Treatments
Surface treatments, such as electrochemical deposition, create micro-patterns that enhance turbulence and significantly improve heat transfer efficiency. Moreover, these treatments reduce fouling and corrosion, ensuring heat exchangers maintain peak performance over extended operational periods. Improved durability from these advancements extends service life, reducing operational costs and downtime for industries requiring reliable systems.
-
Phase Change Materials (PCMs)
Phase Change Materials (PCMs) absorb and release heat during transitions, stabilizing temperatures and optimizing energy use in heat exchangers. For example, PCMs enhance HVAC systems and renewable energy projects by providing reliable thermal energy management solutions. By storing and releasing heat efficiently, PCMs reduce energy demand, support sustainability, and lower the carbon footprint of operations.
Conclusion
Innovations in heat exchanger design enhance efficiency and sustainability, reducing energy consumption and environmental impacts across numerous industries. At Innovative Engineering Solutions, we integrate cutting-edge technologies into projects to help clients achieve superior thermal management systems. Contact us today for insights or assistance upgrading your systems with the latest heat exchanger advancements.
If you are interested in learning more about the science behind heat exchangers, click here to read an article on the topic!