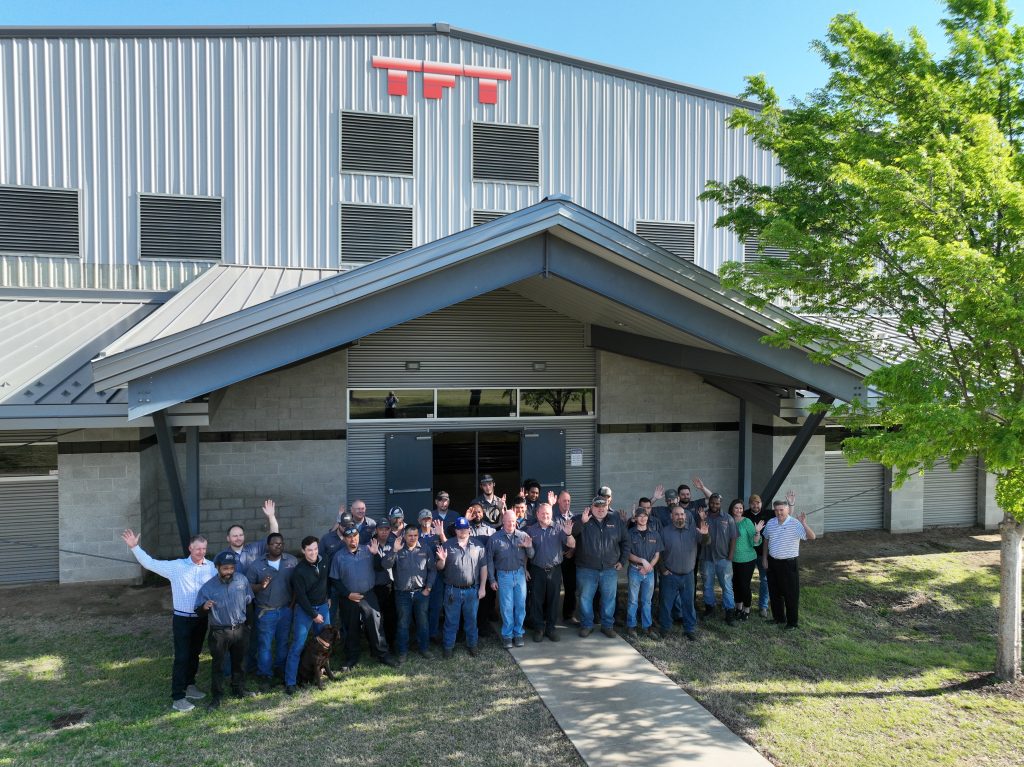
Heat Exchangers: Essential Components for Industrial Operations
In the world of industrial operations, energy efficiency and temperature control are critical to success. Whether you’re operating in manufacturing, power generation, or chemical processing, heat exchangers play a vital role in maintaining system performance and reducing operational costs. At Tulsa Fin Tube, we specialize in designing and manufacturing top-quality heat exchangers that ensure optimal efficiency and reliability for your operations.
What Are Heat Exchangers?
A heat exchanger is a device that transfers heat between two or more fluids—either liquids or gases—without mixing them. They are used to heat or cool a process stream, recover energy, or maintain specific operating temperatures in industrial systems.
Heat exchangers come in various types, sizes, and configurations, each designed to meet the unique demands of different industries. From HVAC systems to power plants, these components are indispensable for efficient thermal management.
Key Applications
Heat exchangers are found in a wide range of industries, including:
1. Manufacturing
In manufacturing processes, heat exchangers are used for cooling machinery, heating fluids, or maintaining precise temperature control in production lines.
2. Chemical Processing
Chemical plants rely on heat exchangers to manage exothermic and endothermic reactions, safely handle volatile substances, and optimize energy usage.
3. Power Generation
Heat exchangers play a crucial role in power plants, where they manage thermal energy in turbines, condensers, and cooling systems.
4. Food and Beverage
In food production, heat exchangers are used for pasteurization, refrigeration, and maintaining sanitary conditions during processing.
5. HVAC Systems
Heating, ventilation, and air conditioning systems depend on heat exchangers to regulate indoor temperatures efficiently.
How They Work
The basic principle of a heat exchanger involves transferring thermal energy from one fluid to another, either to heat or cool the target fluid. This transfer occurs through conduction, where the heat flows through a solid barrier separating the fluids, or through direct contact in specific designs.
Key components of a heat exchanger include:
- Tubes or Plates: Channels through which the fluids flow.
- Shell or Housing: Encases the system to direct fluid flow and ensure proper thermal transfer.
- Fins or Coils: Increase surface area for enhanced heat exchange efficiency.
- Inlets and Outlets: Allow controlled entry and exit of the fluids.
Types of Heat Exchangers
There are several types of heat exchangers, each suited to different applications.
1. Shell and Tube Heat Exchangers
These are among the most common designs, featuring a series of tubes within a cylindrical shell. One fluid flows through the tubes while the other flows around them, making them ideal for high-pressure and high-temperature applications.
2. Plate Heat Exchangers
Consisting of thin plates stacked together, this design maximizes heat transfer surface area and is compact, making it suitable for limited spaces or lower-pressure systems.
3. Air-Cooled Heat Exchangers
These exchangers use ambient air to cool fluids, eliminating the need for water in applications where water resources are limited.
4. Fin-Tube Heat Exchangers
This type uses fins to increase the surface area for heat transfer, making it highly efficient for industrial systems that require high thermal performance.
5. Double Pipe Heat Exchangers
Simple and cost-effective, these feature one pipe inside another, allowing two fluids to flow in opposite directions for efficient heat transfer.
Benefits of Heat Exchangers in Industrial Operations
Heat exchangers are critical to optimizing energy efficiency and system performance. Here’s why they’re indispensable:
1. Energy Efficiency
By recovering and reusing thermal energy, heat exchangers reduce energy consumption and lower operating costs.
2. Temperature Control
Maintaining precise temperatures ensures the quality and consistency of industrial processes.
3. Improved Equipment Lifespan
Efficient cooling and heating reduce wear and tear on machinery, extending its operational life.
4. Environmental Benefits
Heat exchangers reduce energy waste, contributing to sustainability goals and minimizing environmental impact.
5. Customizability
We can be tailor these to specific industrial needs, ensuring optimal performance and compatibility with your system.
Why Choose Tulsa Fin Tube for Your Heat Exchanger Needs?
At Tulsa Fin Tube, we bring decades of expertise and innovation to the design and manufacturing of heat exchangers. Here’s what sets us apart:
- High-Quality Materials: We use premium materials that withstand extreme conditions and ensure long-term durability.
- Custom Designs: Our team works closely with you to create a tailored product that works for your unique operational requirements.
- Cutting-Edge Technology: We utilize advanced manufacturing techniques to deliver precision-engineered products.
- Expert Support: From design consultation to installation guidance, we provide comprehensive support to maximize your system’s performance.
Maintaining Your Heat Exchanger
To ensure your heat exchanger performs at its best, regular maintenance is essential:
- Inspect for Leaks: Check for any fluid leaks that may indicate wear or damage.
- Clean Regularly: Remove debris and buildup to maintain efficient heat transfer.
- Monitor Performance: Track temperature changes and flow rates to detect potential issues early.
- Schedule Professional Servicing: Work with experts like Tulsa Fin Tube for routine inspections and repairs.
Trust Tulsa Fin Tube
When it comes to efficiency and reliability, Tulsa Fin Tube is your trusted partner. Whether you need a custom solution or expert advice, we’re here to help you optimize your industrial operations with top-quality heat exchanger systems.
Contact us today to learn more about our products and services, and discover how Tulsa Fin Tube can help you achieve peak performance and efficiency in your industry.