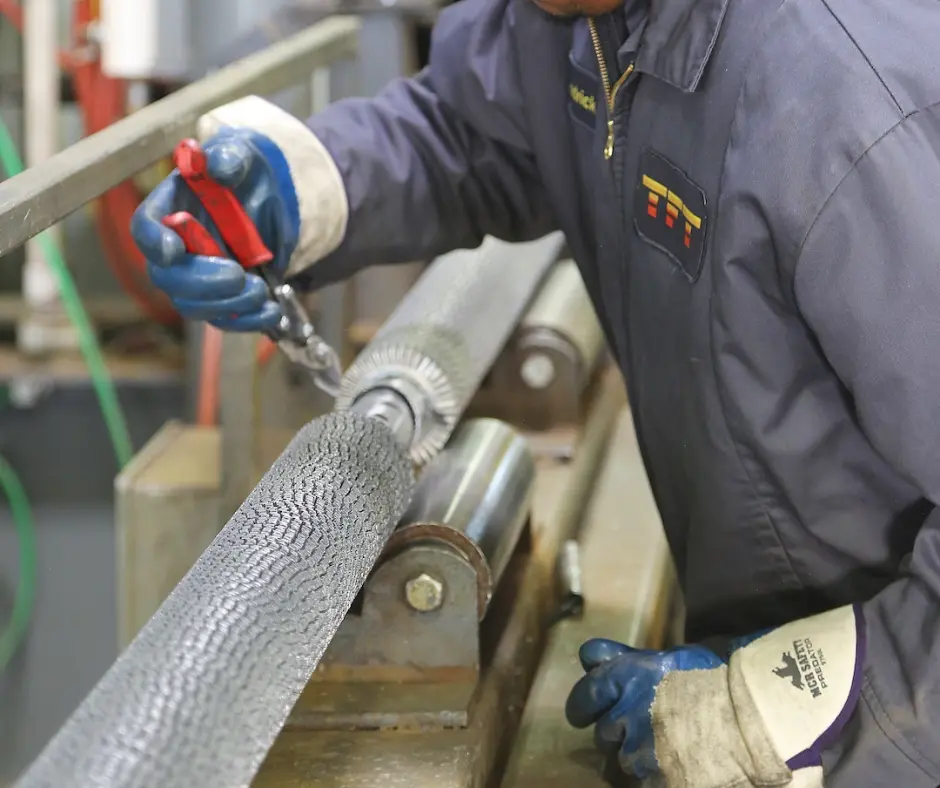
Can Heavy Industrial Tubes Be Customized for Specific Projects?
Diving into the world of heavy industrial tubes, it’s easy to wonder if these robust components can be tailored to meet the unique demands of your project. The answer is not just a simple ‘yes’ or ‘no’. Let’s explore the possibilities together.
Understanding Customization Needs
Customizing heavy industrial tubes involves more than altering their physical features. Instead, it requires a deep understanding of the project’s unique requirements and environmental conditions. Therefore, this approach ensures that customized tubes fit and perform reliably under specific use conditions without compromising effectiveness. Furthermore, identifying customization needs depends on factors like scale, complexity, and precision. For example, high-pressure environments or unusual shapes often require tailored solutions.
Types of Customizations for Heavy Industrial Tubes
Customization options range from adjusting dimensions like diameter and thickness to selecting materials for durability or corrosion resistance. For instance, stainless steel resists rust effectively, while titanium provides strength and lightweight properties for demanding industrial applications.
Additionally, surface treatments, such as galvanization or painting, protect tubes from corrosion and environmental damage efficiently. Specific end finishes also ensure seamless integration with other components. Moreover, internal rifling improves fluid dynamics control in complex systems. Embedded sensors allow condition monitoring, offering advanced solutions for specialized applications requiring precision and innovation.
The Customization Process
Customization begins with consultations between clients and manufacturers to define project specifications, constraints, and timelines clearly. Subsequently, engineers create blueprints or digital models to ensure solutions align with project needs. Afterward, prototypes undergo rigorous testing, allowing adjustments before full-scale production begins. Thus, this process guarantees accuracy and reliability.
Evaluating Your Project Requirements
Evaluating project requirements involves considering performance, durability, and compatibility to ensure the tubes meet specific operational needs. For example, in harsh chemical environments, choosing the right materials becomes critical to prevent corrosion and premature failure.
Finding the Right Manufacturer
Partnering with a capable manufacturer ensures your customization needs are met with precision and quality. Furthermore, a proven track record in custom manufacturing provides confidence in their ability to handle complex requirements effectively. Visiting production facilities and reviewing past projects offer valuable insights into a manufacturer’s capabilities and commitment to quality.
Conclusion
Customizing heavy industrial tubes aligns them with unique project requirements, ensuring efficiency and reliability under challenging conditions. Additionally, partnering with experienced manufacturers transforms essential components into solutions tailored to your specific industrial needs.
If you are interested in learning more about the uses of these industrial tubes, click here to read an article on the topic!