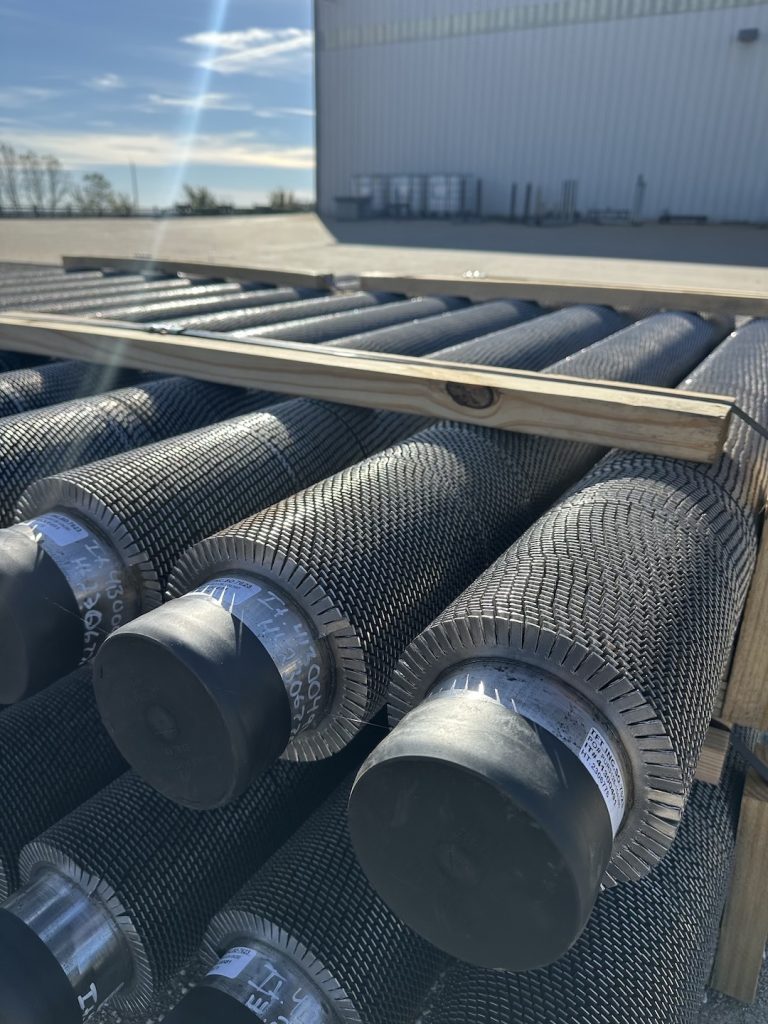
Custom vs. Standard Finned Tubes: Which One Is Right for Your Application?
When it comes to optimizing heat transfer systems, choosing the right type of finned tube can have a major impact on performance, durability, and cost. At Tulsa Fin Tube, we often hear the same question: should I go with a standard design or invest in custom finned tubes? The answer depends on several key factors, including your application’s operating conditions, thermal goals, space limitations, and budget. Let’s take a closer look at how custom and standard options compare—and how to know which is right for you.
What Are Standard Finned Tubes?
Standard finned tubes are pre-designed and manufactured in common sizes, materials, and fin configurations. These off-the-shelf solutions work well for general-purpose applications and are readily available, making them a convenient choice for many businesses.
Benefits of Standard Finned Tubes:
- Faster turnaround times due to pre-existing stock
- Lower upfront cost from mass production
- Proven designs that meet industry norms and certifications
If you’re operating in a stable, low-variability environment like HVAC systems or water-cooled condensers, a standard solution may be more than sufficient. They’re ideal when project requirements are well within the range of what’s already been tested and proven in the field.
However, the drawback to standard designs is that they may not fully optimize heat transfer efficiency or longevity under unique or extreme conditions. That’s where custom finned tubes come into play.
Why Go Custom?
Custom finned tubes are designed and built to match the exact requirements of your system. Everything—from the fin height and spacing to the base tube material and coating—is tailored to meet your operational goals. While the initial cost may be higher, the long-term gains in performance, energy savings, and equipment lifespan can far outweigh the difference.
Advantages of Custom Finned Tubes:
- Optimized heat transfer for your specific fluids, flow rates, and temperature ranges
- Enhanced durability through material selection and protective coatings
- Space efficiency by maximizing performance in compact areas
- Custom geometries to fit non-standard layouts or retrofits
In industries like chemical processing, power generation, or offshore energy, systems often face extreme pressures, corrosive fluids, or unpredictable environmental conditions. A custom solution ensures your heat exchanger is built to thrive—not just survive—in that setting.
Performance Differences That Matter
When comparing custom vs. standard finned tubes, the biggest difference is how efficiently they perform under your real-world conditions. For example, a standard aluminum finned tube might work well in a dry, low-corrosion environment, but would underperform or degrade quickly in a high-salinity offshore setting.
With custom finned tubes, you can select materials like stainless steel or cupronickel to resist corrosion, or tweak the fin density to promote turbulence and increase heat transfer. You can even design tube geometries that reduce pressure drop, which can directly lower operating costs over time.
Factors to Consider Before You Decide
To determine whether custom or standard finned tubes are best for your application, ask yourself the following:
- Are there space constraints? Custom tubes can be designed to fit tight areas without sacrificing performance.
- Is the operating environment harsh? If exposure to corrosive chemicals, salt, or extreme temperatures is likely, customization offers long-term protection.
- Is peak thermal efficiency critical? For systems where energy savings or compact size matter, tailoring your design delivers better ROI.
- Do you need fast deployment? Standard tubes offer speed, which can be crucial for repairs or rapid builds.
- What’s your long-term maintenance plan? Custom tubes may have a higher upfront cost but can reduce downtime and replacement frequency.
Industry-Specific Examples
Consider a petrochemical plant operating in a coastal region. Standard carbon steel tubes would corrode quickly in the salty air, while custom finned tubes made from stainless steel with epoxy-coated fins could last significantly longer.
Or take a data center with limited space for cooling units. A custom high-density finned tube bundle can deliver the necessary cooling without expanding the equipment footprint—something a standard option might not achieve.
Even in the HVAC world, customizations like antimicrobial coatings on copper fins can add value in medical or food processing facilities.
Making the Right Investment
Resources like ASME and Heat Exchanger World regularly highlight innovations in heat exchanger technology and underscore how tailored designs can outperform generic models in the right scenarios. At Tulsa Fin Tube, we use the latest thermal modeling tools and years of application experience to help clients weigh the trade-offs and make smart decisions.
Whether you’re building a new system or retrofitting an old one, the choice between standard and custom finned tubes shouldn’t be made lightly. Your decision impacts performance, reliability, and cost for years to come.
Get the Right Fit for Your System
Every application has its own challenges—and at Tulsa Fin Tube, we specialize in matching the solution to the system. Whether you’re leaning toward the convenience of a standard design or the precision of custom finned tubes, we’re here to help you make the call with confidence. Reach out today and let’s engineer a better-performing future together.