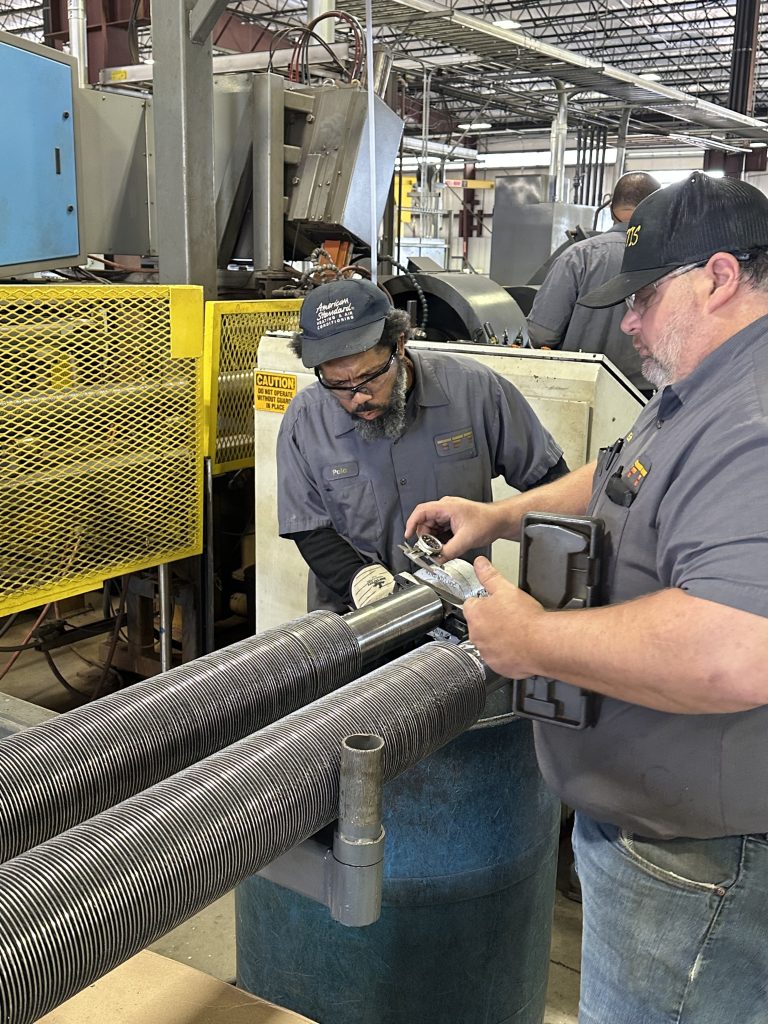
Guide to Heat Exchanger Maintenance: Ensuring Long-Term Performance
Here we will share expert insights into maintaining industrial equipment to maximize efficiency and longevity. Today, we’re honing in on heat exchangers, a critical component in many industries, such as chemical processing, power generation, HVAC systems, and more. These systems play an essential role in thermal management by facilitating the efficient transfer of heat between different media. Proper maintenance of heat exchangers is not just important—it’s crucial for ensuring optimal performance, extending their operational life, and preventing costly downtime that can impact productivity and profitability. This guide offers a comprehensive overview of best practices in heat exchanger maintenance, detailing strategies to keep these systems running smoothly and efficiently for years to come. We’ll cover everything from routine cleaning to advanced monitoring techniques, providing you with the knowledge needed to manage and maintain your heat exchanger assets effectively.
Understanding Heat Exchangers
Heat exchangers are devices that transfer heat between two or more fluids without them coming into direct contact. They are essential for regulating temperatures in a system, making them a critical component in many industrial processes, from cooling large-scale industrial equipment to heating residential buildings. These devices operate by allowing a hot fluid to transfer its heat to a cooler fluid without the two mixing, which is vital for processes that require precise temperature control.
Key Maintenance Strategies
Regular Cleaning
One of the most important aspects of heat exchanger maintenance is regular cleaning. Over time, heat exchangers can accumulate deposits such as minerals, scaling, or sludge, which can impede heat transfer and reduce efficiency. Neglecting to remove these deposits can lead to increased energy consumption and operational costs as the system struggles to maintain the required thermal performance.
- Chemical Cleaning: Utilizing specific chemicals to dissolve deposits. This method is effective for removing scaling and other mineral deposits.
- Mechanical Cleaning: Involves physical methods like brushing or scraping to remove fouling from the heat exchanger surfaces.
- High-Pressure Water Jetting: Uses high-pressure water streams to remove debris and buildup from heat exchanger tubes.
Inspection and Monitoring
Routine inspections are vital to catch issues before they lead to significant problems. Inspections should focus on detecting cracks, leaks, or signs of wear and corrosion. Additionally, these assessments help ensure that all components are functioning within their operational parameters, further safeguarding the system against unexpected failures and prolonging its lifespan.
- Visual Inspections: Regularly scheduled visual checks to identify any signs of leakage or surface degradation.
- Pressure Testing: Performed to ensure the integrity of the heat exchanger. Any drop in pressure can indicate leaks or weaknesses in the system.
- Thermal Imaging: Uses infrared cameras to detect uneven temperature distributions that signify blockages or malfunctions.
Preventative Maintenance
Implementing a preventative maintenance schedule can help avoid unexpected breakdowns and extend the life of heat exchangers.
- Gasket Replacement: Periodic replacement of gaskets can prevent leaks and maintain system integrity.
- Tube Plugging: Defective tubes can be temporarily plugged to prevent leakage until they can be properly repaired or replaced.
- Lubrication of Moving Parts: If your heat exchanger includes fans or pumps, regular lubrication is necessary to ensure smooth operation.
Operational Adjustments
Optimizing operational parameters can significantly impact the longevity and efficiency of heat exchangers.
- Flow Rate Adjustments: Ensuring that the flow rate of fluids in the heat exchanger is optimal can help minimize stress and wear.
- Temperature Monitoring: Regular monitoring of inlet and outlet temperatures helps in assessing the performance and efficiency of the heat exchanger.
Advanced Techniques
- Corrosion Inhibitors: Using corrosion inhibitors can extend the life of heat exchanger components, especially in harsh environments.
- Scale Inhibitors: Regularly adding scale inhibitors to the fluids can prevent the formation of hard scaling on the surfaces.
Conclusion
Maintaining heat exchangers is not just about fixing problems as they arise; it’s about implementing a strategic approach that prevents issues from occurring in the first place. At Tulsa Fin Tube, we understand the critical role heat exchangers play in your operations. By following this guide, you can ensure your heat exchangers continue to function efficiently and effectively, protecting your investment and maintaining your operational capacity. Remember, a well-maintained heat exchanger not only performs better but also saves money in the long term through reduced energy costs and fewer repairs. For more information or assistance with your heat exchanger maintenance needs, reach out to our experts at Tulsa Fin Tube.