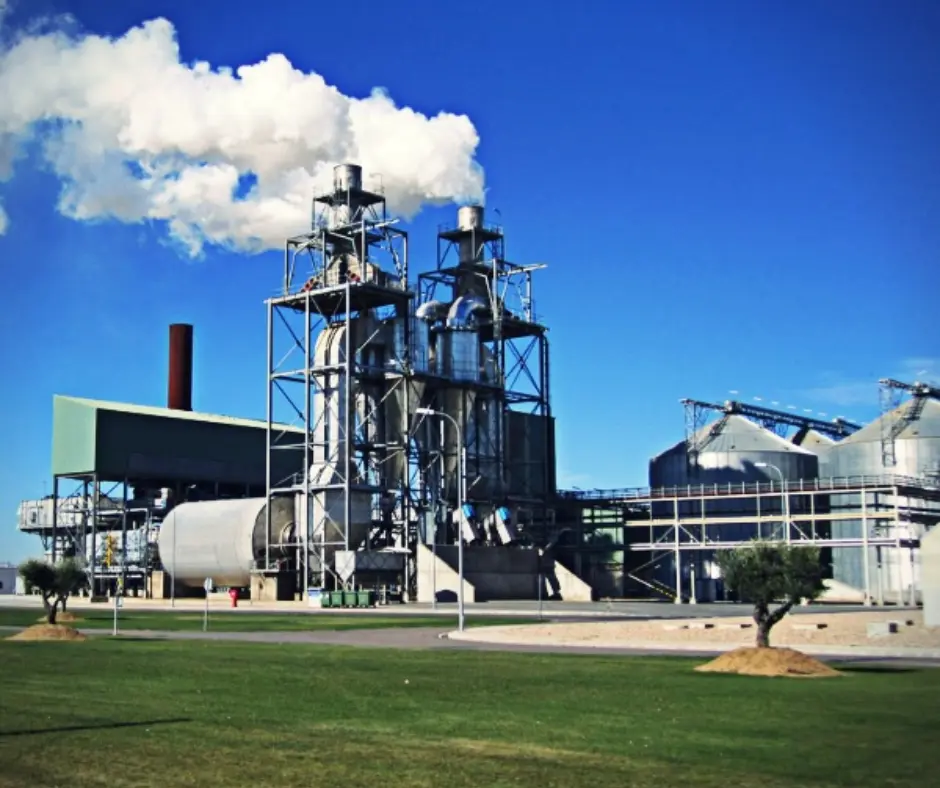
How Do Fin Tubes Improve Heat Transfer Solutions?
Fin tubes play a crucial role in improving heat transfer solutions across various industries. Their design enhances efficiency and effectiveness. By increasing the surface area of tubes, fin tubes improve heat transfer rates without requiring additional space or larger systems. These tubes enable efficient thermal exchange by reducing thermal resistance. This innovation makes them indispensable for modern industrial applications.
The Science Behind How Fin Tubes Improve Heat Transfer
Fin tubes work by attaching fins to the surface of regular tubes, increasing the available area for heat exchange. The added fins disperse heat more effectively, ensuring efficient cooling or heating in processes that demand thermal precision. Thermodynamic principles govern how fin tubes improve heat transfer. The extended surface allows for better heat dissipation and thermal conductivity. Material selection also contributes significantly to efficiency. Aluminum, copper, and stainless steel are commonly used for their excellent thermal properties.
Benefits of Using Fin Tubes in Heat Transfer Solutions
Fin tubes improve heat transfer performance while minimizing energy consumption. This leads to lower operational costs and enhanced sustainability. Their compact design makes them ideal for applications with space constraints. Industries benefit from improved efficiency without increasing equipment size. Corrosion-resistant materials used in fin tubes ensure durability. This reduces maintenance requirements and extends the lifespan of heat transfer systems.
Applications Where Fin Tubes Improve Heat Transfer
The versatility of fin tubes allows them to be used across diverse sectors, including HVAC, petrochemicals, and power generation. In HVAC systems, fin tubes transfer heat efficiently by optimizing air and fluid temperature regulation in compact units. Petrochemical plants rely on fin tubes to handle extreme temperatures and pressure, ensuring optimal performance in demanding environments. Power plants use fin tubes in boilers and heat exchangers, ensuring efficient energy production through enhanced thermal exchange.
How Advanced Designs Maximize Efficiency
Innovative designs like spiral and longitudinal fins improve heat transfer rates by optimizing the flow of fluids and gases. These designs reduce pressure drops, ensuring systems maintain high efficiency while minimizing energy waste during operation. Advancements in coating technologies protect fin tubes from corrosion, further enhancing their performance and longevity.
How to Ensure Optimal Performance of Fin Tubes
Proper installation and maintenance are critical for ensuring effective and consistent heat transfer over time. Regular cleaning prevents fouling, which can reduce efficiency by blocking thermal exchange surfaces. Inspecting for wear and corrosion ensures that systems operate without unexpected failures or reduced performance.
Future Trends in Fin Tube Technology
The future of fin tubes focuses on integrating smart technologies like IoT for real-time monitoring and predictive maintenance. Manufacturers are developing eco-friendly materials and production methods, aligning with sustainability goals and reducing environmental impacts. Enhanced designs continue to emerge, ensuring improvement in heat transfer even in increasingly demanding industrial applications.
Conclusion
Fin tubes improve heat transfer solutions by enhancing efficiency, reducing energy consumption, and ensuring durability. Their applications span numerous industries worldwide. Advanced designs and materials make fin tubes indispensable for modern systems, providing reliable and sustainable heat transfer performance. As industries evolve, fin tubes will remain at the forefront of heat transfer innovation, supporting efficiency and environmental responsibility.
If you are interested in learning more about the science behind fin tubes and how exactly they transfer heat so well, click here for an article on the topic.