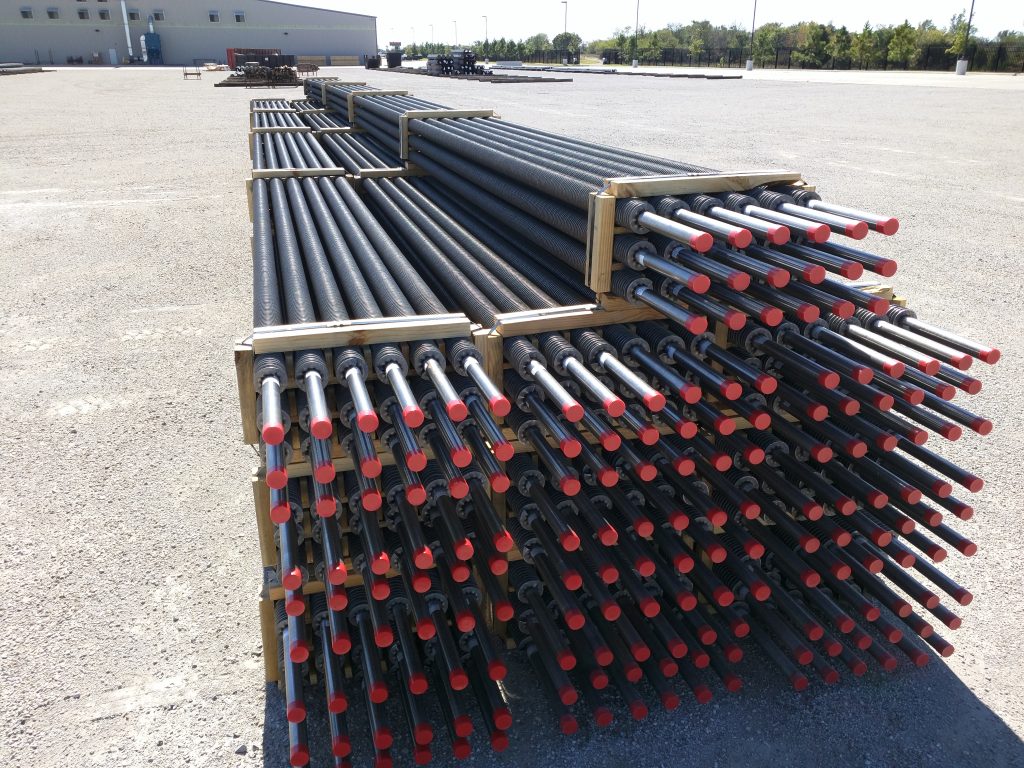
Seamless Tubes in Modern Industrial Applications
Seamless Tubes: Essential for Modern Industrial Applications
Seamless tubes are crucial in modern industrial applications, offering efficiency, safety, and reliability across various demanding industries. Their exceptional strength and durability make them ideal for sectors such as oil and gas, automotive, aerospace, and power generation. Furthermore, their ability to withstand extreme conditions ensures their continued prominence in these industries.
Oil and Gas Industry
In the oil and gas sector, seamless tubes play a vital role in drilling, exploration, and transportation. The high-pressure and corrosive environments necessitate materials capable of enduring without failure. Additionally, seamless tubes made from carbon or stainless steel provide excellent corrosion resistance and mechanical strength.
Their seamless construction eliminates weak points, reducing the risk of failure under pressure. Consequently, seamless tubes enhance safety and efficiency in modern industrial applications like oil and gas exploration.
Automotive Manufacturing
The automotive industry relies on seamless tubes for strong yet lightweight components, improving fuel efficiency and meeting regulatory standards. These tubes are integral in fuel lines, suspension systems, and structural parts, offering durability under high temperatures and pressures.
As electric vehicles rise, seamless tubes will become increasingly essential for precision applications, such as battery and motor components. Therefore, they are indispensable in advancing automotive manufacturing.
Aerospace Engineering
Aerospace engineering demands materials capable of handling extreme conditions. Seamless tubes are used in hydraulic systems, fuel delivery, and structural components, ensuring reliability and performance.
These tubes’ superior strength-to-weight ratio allows lighter designs without compromising safety. Thus, seamless tubes continue to revolutionize aerospace innovation and enhance modern industrial applications.
Power Generation
In power plants, seamless tubes are vital for boilers, heat exchangers, and steam systems. Their ability to endure high pressures and temperatures ensures consistent equipment performance.
By minimizing downtime and maintaining efficiency, seamless tubes contribute significantly to energy production. Consequently, they remain a cornerstone of power generation infrastructure worldwide.
Construction and Infrastructure
Seamless tubes are indispensable in construction, offering strength and durability for bridges, buildings, and industrial plants. They withstand heavy loads and harsh conditions, ensuring reliability in critical infrastructure projects.
Their uniformity and precision reduce failure risks, making seamless tubes essential for modern construction demands. As infrastructure projects grow more complex, their importance will only increase.
Why Seamless Tubes Outperform Welded Tubes
Seamless tubes are preferred over welded tubes due to their uniformity and absence of weak points. This construction ensures superior structural integrity and reliability in high-pressure environments.
Moreover, seamless tubes offer better corrosion resistance and fatigue strength, which are critical in industries requiring long-lasting, high-performance materials. Therefore, they excel in modern industrial applications demanding durability and safety.
Future Trends in Seamless Tube Technology
Advancements in automation, artificial intelligence (AI), and non-destructive testing (NDT) are enhancing seamless tube manufacturing. These technologies improve precision, identify defects early, and ensure product reliability.
Additionally, sustainability is becoming a priority. Manufacturers adopt eco-friendly practices like renewable energy use and waste reduction, minimizing environmental impact. These innovations signify a promising future for seamless tube production.
Conclusion
Seamless tubes are indispensable for modern industrial applications, providing unmatched strength, durability, and reliability. Industries like oil and gas, aerospace, automotive, and power generation rely on these tubes for optimal performance.
As technology advances, seamless tube manufacturing will become more efficient, solidifying their role in critical industries. Their contribution to sustainability and precision ensures their importance in the evolving industrial landscape.
If you need high-quality seamless tubes for modern industrial applications, contact Tulsa Fin Tube. Our products meet rigorous industry demands, offering reliability in challenging environments.
Fill out our contact form to get more information from our professional welders!