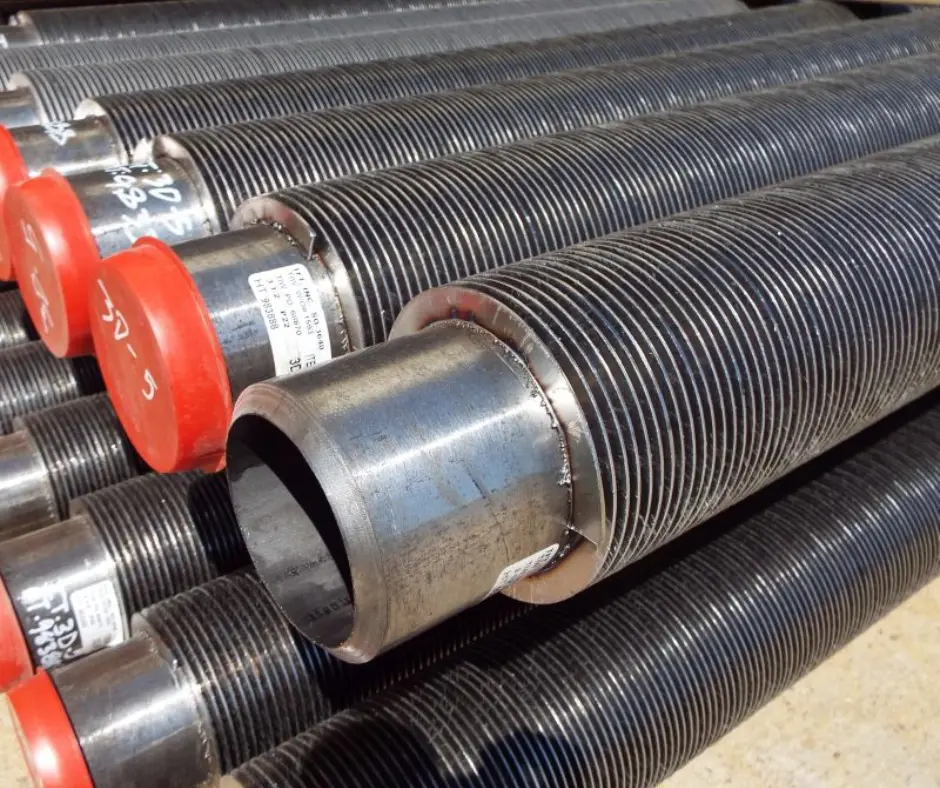
The Essential Guide to Fin Tubes in Boilers | Economizers
What Are Fin Tubes?
Fin tubes are specialized heat exchanger components designed to increase surface area for more efficient heat transfer. These innovative structures play a crucial role in boilers and economizers by facilitating faster and more effective thermal exchange. As a result, they significantly improve heating and cooling performance across various industries.
Although their design appears simple, their impact is substantial. Adding extended surfaces to a tube enhances heat dissipation, making these components indispensable for industries that prioritize energy efficiency. Not only do they optimize system performance, but they also contribute to long-term energy savings.
Why Are These Components Used in Boilers and Economizers?
The primary reason these components are widely used in boilers and economizers is their ability to improve heat transfer efficiency. Within a boiler system, they maximize heat recovery from exhaust gases, effectively reducing fuel consumption and lowering operational costs. In economizers, they preheat feed water, minimizing the energy required to bring water to the desired temperature.
This improved efficiency extends beyond energy conservation, offering economic advantages and environmental benefits. Their role in thermal management highlights advancements in both sustainability and engineering.
Types and Applications
Different variations of fin tubes components cater to specific heat transfer requirements. Common types include Longitudinal, Spiral, and Low-Finned configurations. Longitudinal designs work best in high gas-to-liquid transfer applications. Spiral designs provide enhanced surface area, maximizing efficiency where rapid heat exchange is required. Low-finned options balance performance and cost-effectiveness.
Industries such as power generation, petrochemicals, and HVAC systems benefit greatly from these technologies. Their adaptability ensures integration into diverse applications, making them essential in modern thermal system designs.
How Do These Components Improve Heat Transfer?
The effectiveness of these components lies in their ability to expand the surface area in contact with working fluids. Additional extended surfaces create more pathways for heat dissipation, significantly improving thermal exchange. By reducing insulating boundary layers that form during fluid movement, heat transfer becomes more efficient.
Minimizing these barriers enhances performance, allowing industries to achieve superior energy efficiency. The strategic design of these elements ensures better thermal regulation, outperforming conventional smooth-surface alternatives.
Installation Considerations for Boilers
Installing these heat exchange solutions requires careful planning. Several factors, including boiler type, environmental conditions, and specific thermal needs, must be considered. The process involves not only placing the components correctly but also adjusting other system elements to optimize thermal capabilities.
A successful installation depends on collaboration among engineers, designers, and technicians. Their combined expertise ensures that boilers function at peak efficiency, reinforcing the importance of precision in modern thermal engineering.
Maintenance Tips for Long-Term Performance
Regular maintenance is crucial to sustain efficiency. Routine cleaning prevents debris accumulation, which can insulate surfaces and hinder heat transfer. Techniques such as high-pressure water jetting or chemical treatments help remove stubborn buildups.
Additionally, frequent inspections for signs of corrosion or physical wear enable timely repairs or replacements. Proactive maintenance preserves performance, extending the longevity of both these components and the entire heating system.
Addressing Common Challenges
Despite their advantages, some challenges must be addressed, including increased pressure drops and fouling. Adjusting spacing between extended surfaces helps balance thermal efficiency with pressure requirements. Additionally, selecting durable, corrosion-resistant materials minimizes maintenance concerns while extending operational life.
By implementing well-planned designs and material choices, these obstacles can be managed effectively. A proactive approach ensures that these essential components continue to perform optimally over time.
Recent Innovations in Heat Exchange Technology
Ongoing advancements in this field focus on enhancing efficiency and reducing environmental impact. Nano-coated surfaces improve thermal conductivity while increasing resistance to corrosion. Additionally, modern materials and production techniques have led to stronger, longer-lasting components.
As research progresses, these innovations further strengthen the role of heat exchange technologies in various applications. Staying at the forefront of these developments ensures industries achieve greater sustainability and efficiency.
Looking Ahead: The Future of Thermal Systems
The evolution of these technologies continues to drive improvements in efficiency and environmental responsibility. As integral components in boilers and economizers, they will keep evolving to meet the demands of energy conservation and sustainability initiatives.
Advancing Efficiency in Heating Systems
These heat transfer solutions play a vital role in optimizing system performance by improving thermal regulation, lowering energy consumption, and enhancing efficiency. Their evolving designs push heating technology forward, ensuring a more sustainable future. Staying informed about the latest advancements brings industries closer to achieving peak thermal performance.
Visit our Finning page to learn more today!