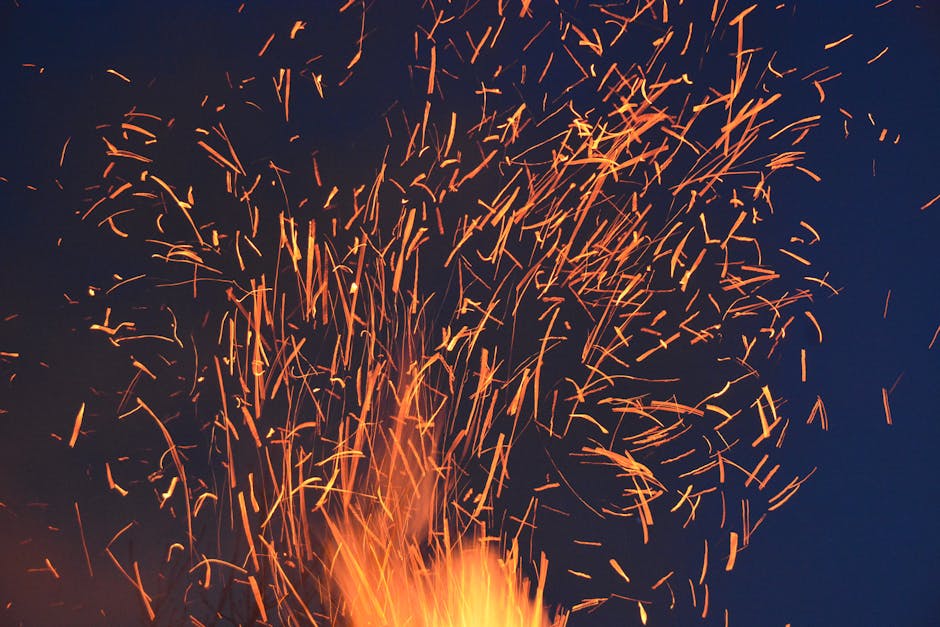
The Science of Heat Exchanger Tubes
When it comes to industrial efficiency, few components play as critical a role as heat exchanger tubes. From their humble beginnings in the 19th century to today’s advanced designs, these steel tubes are not just about transferring heat—they’re about powering industries, conserving energy, and ensuring long-term performance.
At Tulsa Fin Tube, we specialize in manufacturing and welding the high-quality fin tubes that keep heat exchangers working at peak efficiency. Let’s explore the past, present, and future of these vital components—and why the right welding shop in Tulsa makes all the difference.
What Are Heat Exchanger Tubes?
Heat exchanger tubes are the backbone of many industrial systems, transferring heat between fluids while keeping them separated for safety and efficiency.
-
Materials: Commonly made from stainless steel and other corrosion-resistant alloys.
-
Durability: Withstand high temperatures, pressure, and corrosive conditions.
-
Function: Allow hot fluids to warm cooler fluids without mixing.
-
Efficiency: Reduce energy losses, improve reliability, and extend equipment lifespan.
In short, these metal tubes are essential for energy conservation, cost savings, and industrial safety.
A Brief History of Heat Exchanger Design
Heat exchanger tubes have evolved dramatically over the last century:
-
19th Century: Early exchangers were designed for steam engines.
-
20th Century: Shell-and-tube designs became the industry standard, offering versatility and reliability.
-
1930s: Plate exchangers allowed more compact and efficient heating/cooling.
-
1980s: Compact exchangers improved performance in smaller systems.
-
Finned Tubes: Expanded surface area revolutionized HVAC and industrial cooling.
Each milestone was powered by advancements in welding and steel tubing technology, making exchangers stronger, more efficient, and more adaptable.
Modern Innovations in Heat Exchanger Tubes
Today’s exchangers are pushing boundaries with advanced engineering and industrial welding:
-
Corrosion-Resistant Alloys & Graphene – Enhance durability and thermal conductivity.
-
Computational Fluid Dynamics (CFD) – Optimizes flow and efficiency before manufacturing.
-
Additive Manufacturing (3D Printing) – Creates complex tube structures for better heat transfer.
-
Integration with Renewable Energy – Used in geothermal, solar thermal, and waste heat recovery systems.
At Tulsa Fin Tube, our welding experts ensure each fin tube meets strict quality standards, combining precision engineering with decades of Tulsa welding expertise.
The Future of Heat Exchanger Tubes
What’s next for the industry?
-
Nanofluid Technology – Boosts heat transfer at the microscopic level.
-
Smart Exchangers with IoT Sensors – Enables real-time performance monitoring.
-
Sustainable Designs – Integrates renewable energy and waste recovery.
-
Bio-Inspired Engineering – Mimics natural systems for maximum efficiency.
As industries push for greener, more efficient systems, steel tubing and precision welding will remain at the heart of every innovation.
Why Welding Expertise Matters for Fin Tubes
Not all welding shops are created equal. Heat exchanger performance depends on:
-
Precision Welding – Prevents leaks and improves durability.
-
Custom Engineering – Tubes tailored to exact industrial requirements.
-
Local Support – A Tulsa-based partner means faster turnaround and trusted service.
By choosing Tulsa Fin Tube, you gain access to skilled industrial welding professionals who understand the demands of steel tubing and heat exchanger manufacturing.
FAQs About Heat Exchanger Tubes
What industries use heat exchanger tubes?
Energy, HVAC, petrochemical, food processing, and manufacturing all rely on them.
Why choose welded fin tubes over mechanical ones?
Welded tubes offer superior strength, efficiency, and longevity—ideal for demanding industrial environments.
How long do fin tubes last?
With proper welding and material selection, fin tubes can last decades, even under high stress and corrosive conditions.
The Tulsa Fin Tube Advantage
From industrial welding to custom heat exchanger tubing solutions, Tulsa Fin Tube provides the expertise and technology to keep your operation efficient. Whether you need durable metal tubes for energy systems or custom steel tubing for manufacturing, we’re your trusted Tulsa welding shop.
Ready to improve your heat exchanger performance? Contact Tulsa Fin Tube today to learn more about our welded fin tube solutions.