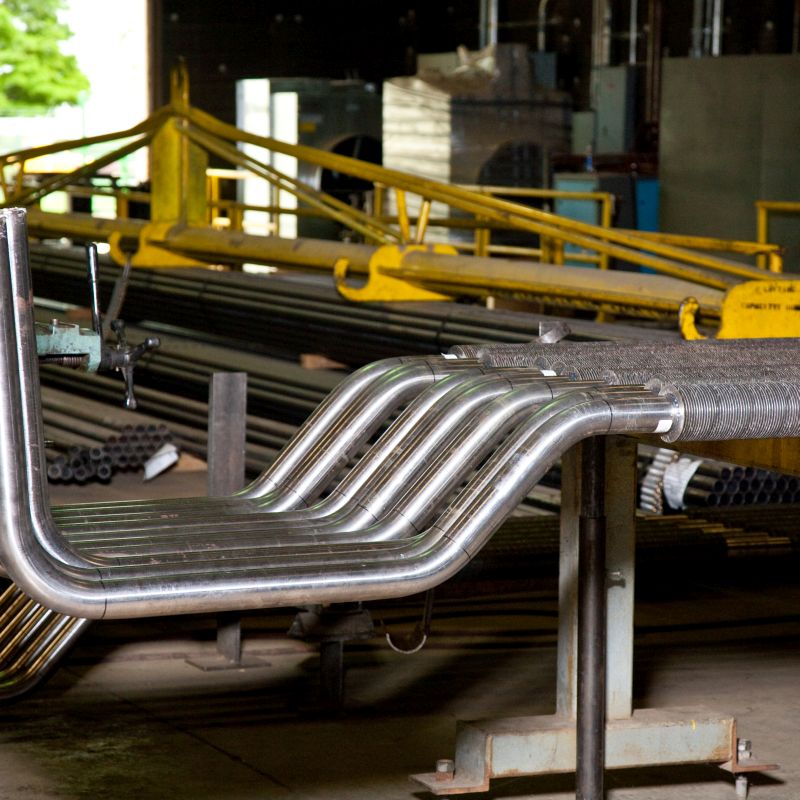
The Role of Tube Benders in Precision Metal Fabrication: How It Works
In the world of metal fabrication, precision is key. Whether you’re working on large industrial projects, automotive components, or delicate architectural designs, the ability to accurately shape and bend metal is essential. We are ready to help you create functional, reliable products. One of the most critical tools in this process is the tube bender. This is a device that allows metal tubes to be shaped with precision and accuracy without compromising their strength or integrity.
At Tulsa Fin Tube, we specialize in custom metal fabrication. Our tube benders play an essential role in the production process. In this blog, we’ll explore how tube benders work, their importance in various industries, and why precision tube bending is crucial for achieving high-quality results.
1. What Are Tube Benders and How Do They Work?
Tube benders are specialized machines designed to bend metal tubing into various shapes and angles. Unlike manual processes, tube benders use controlled forces to manipulate the tube without collapsing or deforming it, ensuring that the tube maintains its strength and structure. This precision is especially important in applications where exact measurements and tight tolerances are required.
At Tulsa Fin Tube, we utilize advanced tube bending technology, including CNC (computer numerical control) tube benders. These machines can handle a wide range of materials such as steel, aluminum, copper, and stainless steel. CNC tube benders allow for automated, highly accurate bends, reducing the risk of human error and ensuring consistency across large production runs.
The tube bending process involves clamping the tube and applying force to bend it around a die that shapes the tube to the desired angle. There are different types of tube bending methods, such as rotary draw bending, roll bending, and compression bending, each suited for specific applications and tubing materials.
2. Applications of Tube Benders in Various Industries
Various industries consider tube benders an indispensable tool, requiring precise bends to meet specific design and functional needs. Their versatility enables use in industries like automotive, aerospace, HVAC systems, and architecture. Below are a few key applications of tube benders:
Automotive Industry:
In automotive manufacturing, technicians use tube bending to create exhaust systems, roll cages, hydraulic lines, and other critical components that require precision to ensure vehicle performance and safety. Tube benders allow for custom shaping to fit specific vehicle designs and configurations, ensuring a perfect fit for every part.
Aerospace:
Aerospace engineers demand extreme precision in tube bending for fuel lines, hydraulic systems, and structural supports, which must meet stringent tolerances and be lightweight and durable due to high safety standards and complex aircraft systems.
HVAC Systems:
Technicians rely on tube benders to shape tubes in heating, ventilation, and air conditioning systems, which transport gases and liquids. These tools are essential for fitting tubes into confined spaces while maintaining efficiency and ensuring proper airflow.
Architecture:
In architecture, tube benders help create aesthetic designs or structural components for modern buildings and installations. Whether shaping curves for handrails or structural beams, tube benders enable architects to realize architectural visions with precision.
Energy and Power Generation:
In the oil, gas, and power generation industries, specialists use tube benders to create piping systems that transport high-pressure fluids and gases. These systems must be built to exact specifications to ensure safety and efficiency under extreme conditions.
At Tulsa Fin Tube, we serve clients across many industries, providing custom tube bending solutions tailored to meet specific project requirements.
3. The Importance of Precision in Tube Bending
In metal fabrication, precision is everything. Even minor deviations in the bending process can lead to structural weaknesses or functional failures. This is why using high-quality tube benders is critical for achieving accurate and consistent results. Precision tube bending ensures that the tubes are bent to exact angles and measurements, without any deformities, wrinkles, or ovalization that could compromise the product’s integrity.
For example, in the automotive or aerospace industries, where tubes often serve as structural components, any inconsistency in the bending process could lead to performance issues or safety risks. The same applies to HVAC systems, where misaligned tubes can result in poor airflow, leaks, or inefficiencies that can affect system performance.
At Tulsa Fin Tube, our tube bending machines are equipped with advanced controls that allow us to achieve the tight tolerances required by our clients. This precision is what sets us apart, ensuring that every part we produce is reliable and meets the exacting standards of the industries we serve.
4. Choosing the Right Tube Bender for Your Project
Choose the right tube bender based on your project’s needs; manufacturers design tube benders with varying capabilities. Tube material, diameter, wall thickness, and bending radius are key factors in selecting the best bending method. For instance, rotary draw benders excel at tight bends with minimal deformation, while roll benders are optimal for large-radius curves.
At Tulsa Fin Tube, we collaborate with clients to pinpoint the ideal tube bending solution for their projects. Our team’s broad experience with diverse materials and configurations equips us to tackle complex bending challenges.
For precision bends in high-performance automotive parts or custom tubing for infrastructure, rely on our experts for outstanding outcomes.
5. Quality Control and Testing
Ensuring the final product meets industry standards and client specifications is crucial in tube bending. It’s essential to inspect and test tubes for accuracy and strength after bending. High-quality benders provide consistent bends, but further quality control is necessary to ensure each piece meets standards.
At Tulsa Fin Tube, we perform thorough inspections and testing to meet all safety and performance requirements. Our procedures include dimensional checks and pressure testing, ensuring no detail is overlooked. Our commitment to quality has earned the trust of clients in various industries.
Tube Benders in Precision Metal Fabrication
Tube benders play a pivotal role in modern metal fabrication. This enables the creation of custom, precision-engineered tubes for a variety of applications. From the automotive industry to aerospace, HVAC systems, and beyond. The versatility and precision of tube bending make it an essential process for achieving high-quality metalwork.
At Tulsa Fin Tube, we pride ourselves on providing top-tier tube bending services. We meet the diverse needs of all of our clients. We have advanced equipment, an experienced team, and dedication to quality. Always, we ensure that every project we complete holds to the highest standards. Whether you’re looking for custom tube bending or need assistance with a complex fabrication project, we’re here to help.
Contact Tulsa Fin Tube today to learn more about how our tube benders can provide these precise solutions.