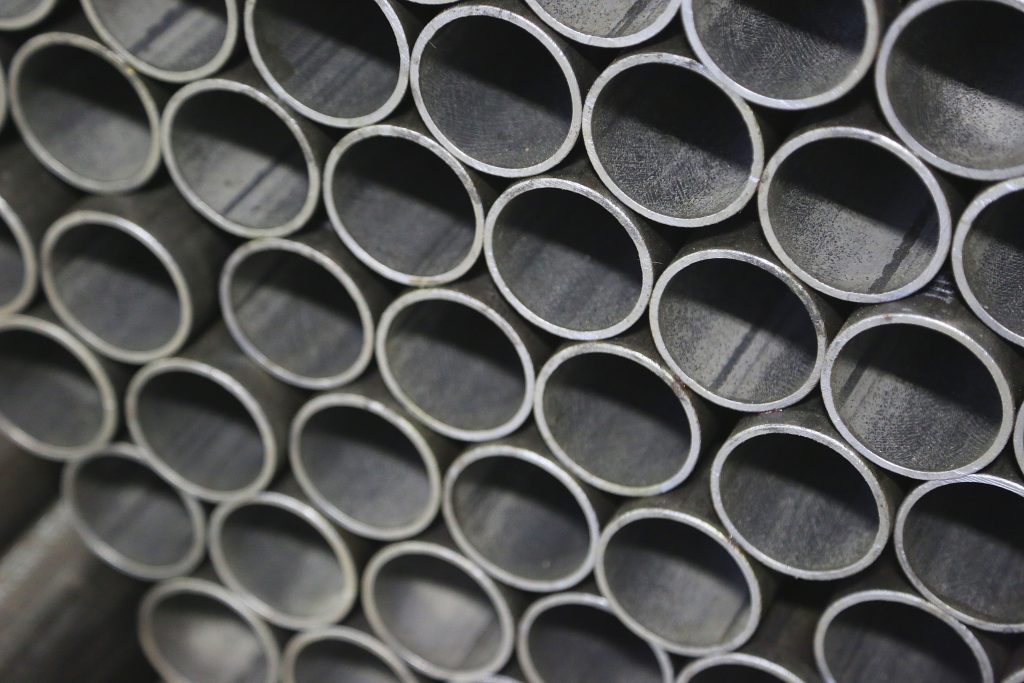
When to Use Finned Tube Heat Exchangers
Finned tubes are great for improving heat transfer in industrial systems.
They work by adding to the outside, which increases the surface area and makes heat transfer more efficient.
Finned tube heat exchangers are especially useful when you need to transfer heat between fluids. Here’s when they’re a good option:
High-Efficiency Heat Transfer Requirements
Finned tube heat exchangers are ideal when there is a need for enhanced heat transfer efficiency. The fins significantly increase the surface area, allowing more heat to be transferred between fluids.
This makes them particularly useful in industries where optimizing thermal efficiency is critical, such as power plants, HVAC systems, and petrochemical processing. Knowing when to use finned tubes can lead to significant improvements in energy efficiency.
Handling Large Volumes of Air or Gas
When your application involves the heating or cooling of large volumes of air or gas, finned tube heat exchangers are the go-to solution.
Their design allows them to efficiently manage air or gas flows by maximizing the contact surface area, which is essential in air-cooled heat exchangers, economizers, and industrial air conditioning systems.
Understanding when to use in these contexts is key to achieving optimal performance.
Limited Space with High Heat Load
When space is limited but the heat load is significant, you can rely on finned tube heat exchangers as a compact and effective solution.
The fins increase the surface area, allowing a smaller exchanger to achieve the same heat transfer as a larger, non-finned unit.
This makes them highly suitable for applications in confined spaces, such as automotive and aerospace industries.
Recognizing when to use finned tubes in space-constrained environments can greatly enhance system efficiency.
Corrosive or Harsh Operating Conditions
You often use finned tubes in environments where fluids may be corrosive or operating conditions are harsh.
Manufacturers design the fins from corrosion-resistant materials, such as stainless steel or aluminum, to ensure long-term durability and reliability.
This makes finned tube heat exchangers ideal for chemical processing plants and marine applications.
Knowing when to use finned tubes in such environments is crucial for maintaining system longevity.
Cost-Effective Heat Recovery
Finned tube heat exchangers are also utilized in scenarios where cost-effective heat recovery is essential.
By improving the efficiency of heat transfer, these exchangers can reduce the energy required to heat or cool fluids, leading to significant cost savings.
This is particularly beneficial in applications like waste heat recovery systems and industrial dryers.
Understanding when to use for heat recovery can result in substantial operational savings.
Versatile Applications Across Industries
The versatility of finned tube heat exchangers means they are used across a wide range of industries.
Whether it’s for preheating fuel in power generation, cooling hydraulic oil in heavy machinery, or condensing steam in food processing, these exchangers provide reliable performance in diverse environments.
Knowing when to use finned tubes ensures that your application benefits from the most efficient heat transfer solutions available.
Conclusion
Use finned tube heat exchangers when you need high-efficiency heat transfer in applications involving large volumes of air or gas, limited space, harsh conditions, or cost-effective heat recovery.
Their versatility and efficiency make them a preferred choice across multiple industries, ensuring optimal thermal management and energy savings.
If you’re considering upgrading or designing a new heat exchange system, understanding when to use is key to achieving superior performance.