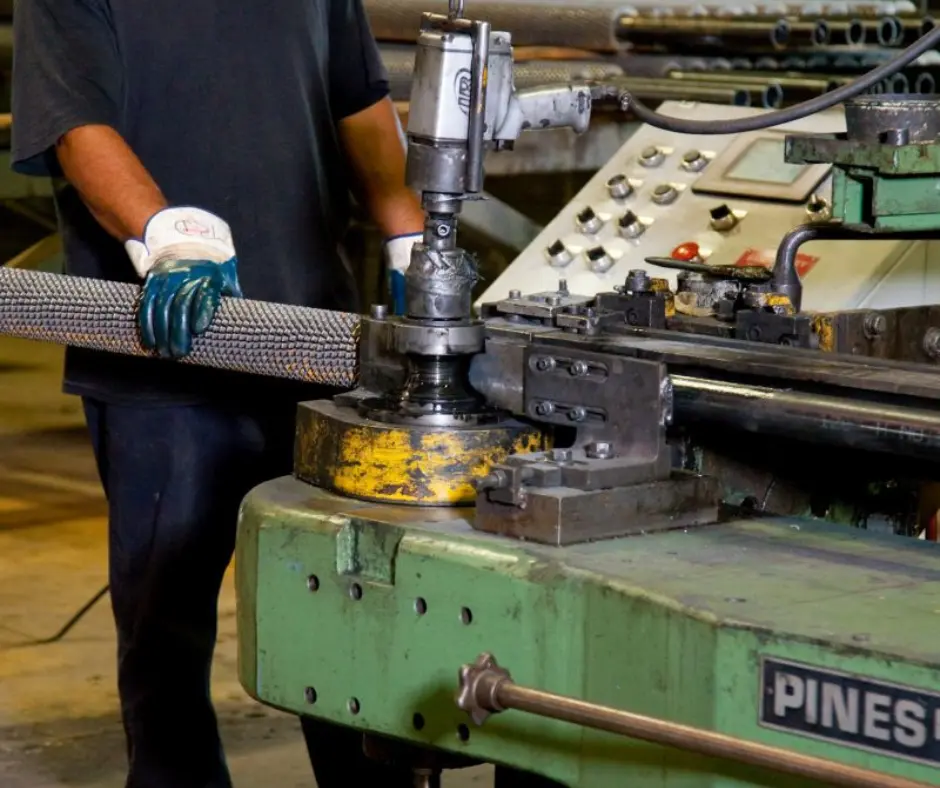
What is the Quality like on Welded Fin Tubes?
Delve into the world of fin tubes and discover the critical role welding plays in determining their quality, performance, and durability.
Understanding Welded Fin Tubes
Welded fin tubes drive efficiency in heat exchange applications, enhancing surface area and heat transfer capabilities across various industries. Manufacturers attach fins to tube surfaces through welding, significantly boosting the tubes’ ability to heat or cool efficiently. Proper welds reduce thermal resistance, directly impacting tube performance and ensuring maximum heat exchange.
Engineers commonly use materials like stainless steel, carbon steel, and alloys to fabricate welded fin tubes. Each material presents unique welding challenges.
Types of Welding Processes for Fin Tubes
Fabricators use several welding techniques to produce welded fin tubes, including High-Frequency Resistance Welding (HFRW) and Submerged Arc Welding (SAW). HFRW efficiently produces high-quality welds, making it ideal for mass production. In contrast, SAW creates deep penetration welds suitable for thicker materials.
Metal Inert Gas (MIG) welding offers flexibility, enabling complex applications for fin tubes across diverse industries.
Impact of Welding on Durability
The welding process determines the durability. Poor welding creates weak points, increasing failure risks under stress. Improper techniques can also reduce corrosion resistance by altering the metal’s structure, shortening the tube’s lifespan in corrosive environments. Selecting the right welding method ensures reliable performance under demanding industrial conditions.
Welding Techniques and Performance
Advanced techniques enhance welded fin tube performance by improving heat transfer efficiency and minimizing energy losses. Effective bonding between fins and tubes remains critical for maximizing heat exchange capabilities.
Quality Assurance in Fabrication
Quality assurance procedures rigorously test tubes, ensuring welds meet high standards. Inspections include visual checks, non-destructive testing (NDT), and sometimes destructive testing for structural integrity. Strict quality control reduces defects, boosting efficiency and reliability.
Common Issues and Solutions
Defects like porosity and incomplete penetration threaten the performance of fin tubes. These issues increase the likelihood of failure. Adjusting welding parameters, enhancing operator skills, or using alternative techniques addresses these problems effectively, ensuring robust and reliable tubes.
Future Trends in Welding Technology
Advancements in technology transform fin tube manufacturing. Automation and artificial intelligence (AI) increase precision and detect defects early. Non-destructive testing further guarantees quality, while eco-friendly manufacturing practices reduce environmental impact, meeting sustainability goals.
Conclusion
They remain essential for efficient heat exchange applications. Industries depend on their durability and reliability to meet operational demands. By integrating advanced techniques and maintaining strict quality assurance, manufacturers deliver tubes that satisfy evolving industrial needs.
Contact us today to learn more about our high-quality welded tubes. We offer tailored solutions to meet your industrial needs. If you are interested in learning more about the many uses of finned tubes, check out this article here!